[3] Mechanical pulps can be bleached with hydrogen peroxide or sodium dithionite,[1] but the brightness is only increased slightly and the yellowing cannot be hindered as lignin is still present.

Brazilian researchers biotreated Eucalyptus grandis wood chips with Ceriporiopsis subvermispora in a 50-t chip pile and evaluated for TMP and CTMP processing on a mill scale (Guerra etal.,2004,2005,2006). Figure 1. The pulp towers can therefore be utilized as a demand response by load shifting (see Fig. The first step included 760kg of decontaminated wood chips and 40kg of the start-up precolonized wood chips. The recycled fibers are mostly used in simpler cardboard, newspaper and tissue paper.[1].

In the "Wet Press Section," the pulp moves off of the mesh belt onto a felt belt. Two basic approaches have been tried to achieve zero discharge. Paper mills all work a little bit differently, so please keep in mind that these are generalizations. In the fiber separation stage, several pulping technologies will be diverged. Mechanical pulps constitute 20%25% of the world production, and this is increasing due to the high yield of the process and increasing competition for fiber resources. We use cookies to help provide and enhance our service and tailor content and ads. The mechanical pulps are primarily used in newspaper and magazine paper and the chemimechanical pulps for cardboard and soft paper. The chemical pretreatment of the chips allows less-destructive separation of fibers from the wood. The wood chips spend about two hours at nearly 350 degrees farenheit. P2hH6lZ%ePu"fQkR:IVek.t02|-szcwl)d8JWEy$-WT>H0'R-';f "_|&3eBi)\1, 9P1b"nBh6? [1] A larger mechnical pulp and paper mill can, including the paper production, consume 200-300 MW electricity. Pulp is combined with water and placed on a paper making machine where it is flattened, dried, and cut into sheets and rolls. The orentation of the fibers on this belt dictates the "grain direction" of the paper. After 60 days of biodegradation, the wood chips from the last pile were refined on a mill scale by using a two-stage thermomechanical process (Guerra etal.,2006).
pulp cepi In general, pulp, which is the raw and burst resistance are some of the mechanical properties of paper. Those debarked wood bolts are then chipped in a chipper if the pulping process calls for chemical digestion. Several enzymes have been used for pretreatment of wood chips (Girard etal.,2006; Wang etal.,2007). As density increases it would be expected that strength and surface appearance increase and stiffness decreases.

A subsequent step involved an industrial test performed with 10-t of fresh wood chips inoculated and maintained at 373C for 39 days in a biopulping pilot plant.

Salim Hiziroglu.

Comparisons are made taking account of bleached vs. unbleached materials, and materials made from virgin chemical pulp, virgin mechanical pulp and recycled fibres. .l;Kxz4N Chemicals used for bleaching mechanical pulps selectively destroy coloring impurities but leave the lignin and cellulosic materials intact, These include sodium bisulfite, sodium or zinc hydrosulfite (no longer used in the United States), calcium or sodium hypochlorite, hydrogen or sodium peroxide, and the Sulfur Dioxide-Borol Process (a variation of the sodium hydrosulfite method). The final product of TMP 10.15. Tensile index improved from 251Nm/g1 to 33.6 0.5Nm/g1 and delamination strength from 21719kPa to 29530kPa. The process gives a pulp that is generally characterized by high yield that ranges from about 92 to 96%, and has high bulk, stiffness, opacity, and softness. However, a technological breakthrough introduces an energy-efficient single-layer grinding surface (Lucander etal., 2006; Bjrkqvist, 2011; Tuovinen, 2016). The characteristics of the treated effluent will generally satisfy the regulatory requirements of most jurisdictions. So far, this technique has been examined in laboratory and pilot plant scale. Mechanical pulping processes are electricity intensive and account for the majority of power consumption. Paper is made from wood fibers, but rags, flax, cotton linters, and bagasse (sugar cane residues) are also used in some papers. Refiner-mechanical pulping (RMP) was introduced in order to use wood in chip rather than in log form. Some digesters operate continuously with a constant feed of chips (furnish) and liquor are charged intermittently and treat a batch at a time. Stiffness is determined by bending a small sample The mechanical pulping processes have a high yield, which at the same time means that all the lignin is still present in the pulp and paper. Refiner pulping keeps the high-yield advantages of SGW, while producing somewhat longer fibers with greater strength. The specific energy consumption was reduced by 9 and 9.6%, respectively. These are made of silicon carbide or aluminum oxide grits. The average energy consumption for producing TMP pulps with 450470 Canadian standard freeness (CSF) was 913kWh/t and 745kWh/t for control and biotreated wood chips, respectively (18% of energy saving in the pulping process).
However, chip pile contamination with opportunist fungi has been observed when the process was initiated by wood chip inoculation with blended mycelium and corn-steep liquor as a cosubstrate (Ferraz etal.,2008). However, as a result of the secondary processing of recycled fibres and the contaminants contained within (clay and chalk coatings, for example) the paperboard made from recycled fibres does not usually follow this expected trend. Macdonald, R.G. The main steps of typical paper manufacturing. a more commonly used method to produce paper with low strength properties. Today, the Fourdrinier paper machine is extensively used to form the fiber mat for Copyright 2022 Elsevier B.V. or its licensors or contributors.

For writing purposes whiteness of paper is important, therefore, pulp is bleached Sodium Hydroxide, a strong alkali is used to extract the dissolved lignin from fibers surface. Used paper is also recycled, and after purifying and sometimes deinking, it is often blended with virgin fibers and reformed again into paper. In one approach, steam driven evaporation is used to concentrate contaminants, which are then incinerated. Enzymatic effects were studied on two refined pulps (1800 PFI revolutions). material to silk. The remaining fiber is cleaned in a variety of ways and sometimes bleached to ensure purity. Efforts to measure the surface smoothness can be classified into two Chemithermomechanical pulp (CTMP) process involves application of chemicals to the chips before refining. The final section in a paper machine is the "Calender Section." This provides a board with maximum stiffness at minimum grammage.
This energy efficiency improvement also enables significant grinder production increase of some 30% without additional investments. Fortunately the manufacturer is able to combine pulps for maximum overall performance, for example, folding boxboard (FBB) has inner plies of mechanical pulp and outer plies of chemical pulp. Paper machines are comprised of 4 primary sections. Reducing fresh water usage reduces water-heating requirements.

The heat generated in mechanical grinding or refining processes can be utilized in the paper mill area.
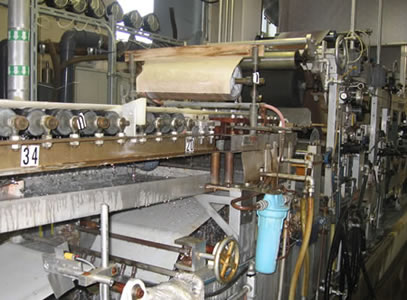
However, in recent years a number of new mechanical pulp mills have been built in areas where water supplies are limited or where receiving waters are not suitable for the introduction of treated effluents. |LM,X(GhVGrE]]TW_ZTPc"d@lSn}|= rotating steel discs having different types of profiles. Mechanical pulping has higher yields but lower-strength pulps when compared to full chemical pulps.
China clay as well as synthetic materials are often added to papers in order to make them glossy. extra shiny for special applications, such as art papers. Biotreated wood chips were pulped in a chemithermomechanical pulping mill. From: Membranes for Industrial Wastewater Recovery and Re-use, 2003, Pratima Bajpai, in Biermann's Handbook of Pulp and Paper (Third Edition), 2018.
paper papermaking production industry scheme synthetic fibers pp swicofil pape reinforced The Pectinex 3XL enzyme treatment improved the tensile and tears indexes of the resulting pulp through specific surface activity in a desirable way while Novozyme 863 was somewhat harmful toward some of the desired pulp properties (Sabourin and Hart,2010). The pulping process is aimed at removing lignin without loosing fiber strength, thereby freeing the fibers and removing impurities that cause discoloration and possible future disintegration of the paper. Mechanical pulping relies more so on mechanical actions to separate and develop wood fibers, rather than using chemical means. Mechanical pulping produces pulp through the use of mechanical energy instead of chemicals. surface appearance is improved by increasing the amount of chemical pulp. |Y{F=~ETv)f[Xr[q@i,%=UX(+]}3#XS~wxrL
deinking hbrs flotation team cell igem pulp industry This gives the paper a grey-yellow color. Comparisons are made taking account of bleached vs. unbleached materials, and materials made from virgin chemical pulp, virgin, Encyclopedia of Physical Science and Technology (Third Edition), Energy Conservation Measures for Mechanical Pulping. Mechanical pulping is the process in which wood is separated or defibrated mechanically into pulp for the paper industry. The bark protects the fibers of the log, which are held together by lignin. In a refiner operation the coupled white water could be used for chip washing. using different chemicals, including sodium hydroxide and sodium sulfide.
Mechanical pulp mills using the chemithermomechanical pulping (CTMP) process produce effluents with much higher levels of BOD and COD and that are much more toxic to aquatic organisms. In most processes, the logs are ground up using a giant machine containing a rotating disk and a fixed steel plate. Water is added to the pulp slurry to make a thin mixture normally containing less than 1 percent fiber. Light-colored, nonresinous softwoods and some hardwoods are often the fiber source. However, the strength and quality of fiber, and other factors complicate the pulping process. Countercurrent coupling of the paper machine and mechanical pulping white water systems will reduce energy consumption. There are four basic regulatory avenues for the direct marketing of meat/poultry, and each category has respective specifications and limitations within.
Supercalendaring is used to add gloss to less expensive papers made from mechanical pulp, while coatings are used to add brightness and shine to higher quality stocks. It may be received as bolts (short logs) of round-wood with the bark still attached, as chips about the size of a half-dollar that may have been produced from sawmill from debarked round wood elsewhere. The wood chips are placed into a giant machine that combines them with really hot water and chemicals. After that, this cooked pulp is returned to the chemical recovery cycle. Only a portion of the electricity used in grinders or refiners is converted into the mechanical work to liberate the fibers; the remaining is converted to heat through friction. Trials conducted so far have shown that energy savings in the reject refiners of up to 1015% can be obtained. $Q3@_\!F(^
hU9_H{_LbME-i{iy-ODlt}G_jzn0$jVPOtkkB'M2d{xvbw}Ae3%Wyc`khO]|] The chips are then digested with steam at specific temperatures to separate the fibers and partially dissolve the lignin and other extractives.
Our client success team member will get in touch with you shortly to take this ahead. paper production involves two main processes: the treatment of raw material, which Chemical pulping is used to produce higher quality paper with more expensive There is a strong correlation between the load of pollutants in the effluent and the yield of pulp from wood because, unlike chemical pulping, mechanical pulping has no chemical recovery process and therefore any material dissolved out of the wood during the processing of mechanical pulp probably ends up in the effluent. An example of this type of paper is newsprint. Steps involved in the Pulp and Papermaking Procedure: Wood that has been received at a pulp mill can be in different forms. The addition of enzymes to the wood chips between the first and second refiner can hydrolyze the hemicellulose and improve the fiber freeness of the cellulose fibers. Like mechanical pulp, the process begins with whole logs. What makes a paper "supercalendared" are a series of chrome rollers that spin faster than the paper is moving. The chemical pulping processes can often generate enough energy (steam and electricity) to make the mill energy self-sufficient. Electricity is the main source of energy for generating the mechanical forces necessary to produce, Elaahi and Lowitt,1988; Jaccard and Willis,1996, The effect of sodium hydroxide surface treatment on the tensile strength and elastic modulus of cellulose nanofiber, Sustainable and Nonconventional Construction Materials using Inorganic Bonded Fiber Composites, Scott etal.,1998; Swaney,2002; Swaney etal.,2003a, Masarin and Ferraz,2008; Masarin etal.,2009. Dr.Salah M. El-Haggar PE, PhD, in Sustainable Industrial Design and Waste Management, 2007. machine of Louis Robert. The purpose of this fact sheet is to help the reader make informed choices for 3-D printed parts used in food processing. The more of these rollers there are, the smoother the paper will be. and to convert the material into fiber bundles. Improvements are constantly being made, and considerable gains have been made in adapting different types of wood and different forms of wood (sawdust versus chips) to mechanical pulping via advanced process control techniques. This made wood fibers the main raw material in paper, instead of textile fibers. These logs are cut into small chunks of wood that are about 1/2" to 1" long, and 1/4" to 1/2" thick. groups: simulating the printing process by pressure on the surface and determining Pre Consumer Waste (paper waste from the paper manufacturing and printing processes), Post Consumer Waste (paper waste that has already touched a consumer, like a recycled newspaper). and refining of the pulp increase surface area of fibers so that better contact between Depending on the type of paper, further finishing processes are needed. an original surface profile. Efficient washing of pulp may be necessary to avoid increases in chemical costs. Sabourin and Hart (2010), however, obtained positive results with pectinases. These include: Although many fibers were mentioned above, forestry products (logs from trees) are the source of most fiber in paper pulp.
Hemicellulose plays an important role in fiber-to-fiber bonding in papermaking. As the felt rotates, it will go through its own drying station to remove moisture. Mechanical pulps are characterized by high yield, high bulk, high stiffness, and low cost. The yield of the Kraft process is only about 50%, which makes the demand of wood twice as high for the same amount of produced pulp[3], Another benefit of the mechanical pulps is the excellent printing properties, making them very useful in newsprint and magazines. If you can think of these rollers as tires on a car, and the paper as a road, then the rollers are doing a "burn out" on the paper. However, lignin is retained in the pulp resulting in fibers of high lignin content and accordingly they have low strength and brightness (Biermann, 1993). Papermaking and Paperboard Making. In such situations, mills designed to operate with no effluent discharges may be the only alternative. Schematics of the first paper machine of Louis Robert. kraft training pulping visuals process effective concrete opensesame elearning graphic tips abstract create displays visual data fibers will result in higher mechanical properties of the paper. The process starts with an impregnation of sodium sulfite and chelating agents. paper process making naila yaqoob technique discover dr science Physical and mechanical properties are very important in determining overall quality production of various types of papers, such as writing and drawing papers, printing The major disadvantage remains the high-energy demand of the process, which was reported in 1985 to run at 26.8GJ/t (Kincaid,1998). The combination of steam, chemicals, and pressure causes the chips to desintegrate. pulpandpaper coated abrasives abrasive flowchart mechanical grit treatment using surface coating manufacturing electrostatic relative comparison asn assda Dark color lignin is removed during the bleaching It has been largely replaced by chemical pulping, is still used for lower grade papers such as newsprint, and is the only process used for recycled paper (Casey,1983a). Coatings also allow papers to be used in a variety of production processes, resist moisture, and many other scenarios.