
At leastdeficiencies in the motors current sensing path should affect the positioning more uniformly. .bpro-blog a{color:#ffffff;}
Exceeding this smaller, incremental torque wont result in step loss, but it will cause the same absolutepositioning error of up to 2full-steps. Ryan, I just checked out your Excel simulator. I didnt mean for anyome to build a 1:16 ratio physical system on an actual levers or belts. I read datasheets if I DESIGN something. If its any consolation, the Wantai motor brand used here is a relatively commonly used in DIY 3D printers and it appears to stack up pretty well. Seems like if there were no bearings in the motor, other atomic-scale wear through a rotation, things should be setup pretty darn similarly each time. This results in a step angle of 1.8 , respectively 0.9 . Gears will be better, because you will get more torque. Sonny Lloyd has added a new log for Axiom: 100+kW Motor Controller. We have cooperated with more than 30 international leading companies worldwide and provided them creative solutions and high quality products which are efficient, energy saving and environmental. You need to switch it to fast decay mode if you want proper microstep spacing. JavaScript seem to be disabled in your browser. But this is discussed more in depth in the linked article. Great write-up Id love to see more of this sort of thing. According to the above table, this motor should be capable ofaccurate positioning with a 16 microsteps per full-step driver. For the test setup, I borrowed the red laser pointerfrom myIR thermometer and attached it to the motor through a 3D printed fixture.

Even though it only delivers 1 A per phase, itachieved very linear, equally spaced microsteps in the unloaded test, with small but reproducible deviations from the ideal position within 1microstep. .bpro-12{margin-bottom: 15px;width:15%;float:left;font-size:14px;color:#fff;}
stepper powerplus torque moonsindustries Thanks!
stepper nema17 34n so can I be an ass and just ask what microstep everyone is using on theyre drv8825s? Combining the cutting-edge technologies developed by the leading motion control brands of AMP, Lin Engineering and Technosoft, MOONS' has comprehensive capabilities to continously provide all-purpose innovative solutions to the most demanding applications for thousands of customers around the world. Yes, fast decay hurts my ears too. Backlash is caused by "slop" or "play" between the threads on the nut and the threads on the lead screw. Yes, I did. .bpro-blog span{display:block;line-height: 26px;margin:5px 0 0 25px;}
When trying to find the right motor and size it's important to keep in mind the application the motor will be used for as well as the power you can provide to the motor. But with higher speed and therefore higher inertial load the vibrations reappeared. They were all on the maximum current that they would deliver without heatsinking on the same motor. .pbcn_yellow{color:#FFFF00 !important;font-weight:bold;}
But what is a stepper motor, and how does it work? But more importantly, it looks like the load deflection is roughly 1 here, which is a little bit more than half of a physical step, (or 8 microsteps here) assumed it is a 1.8 per step motor that was used. We also seem to be in a market where $10 extra cost to the machine is simply intolerable. This can be calculated one of two wayseither by dividing the motor's full 360 degrees by the number of steps the motor takes to complete one revolution, or by dividing the motor's full 360 degrees by two times the number of rotor teeth times the number of stator phases (Fig. and when they come having a built in which has a good home cinema. Good to know! (Read been pulling them out of the dust bin and trying different configurations every once in a while). -->
I dont remember much about our results except that typical step motors were very non-linear between full steps. The datasheets have quite a bit to say about choice of decay modes that Ive not yet deciphered, but this has given me a good framework for sorting things out. Available torque is already exhausted. printing traces on a PCB at right near the minimal-full-step-tolerances for the stepper E.G. It might not be enough of a difference but stallgaurd 2 might change things. Pretty interesting. Everything has its limits of course, but if you are moving small things, the motors magnetic cogging does just fine to hold position. This allows others to repeat the tests under comparable circumstances. My use is: a mpcnc but I use a cnc usb controller board and drv8825 drivers combo instead of the usual ramps. Ok, Just poured through all the comments. In order to improve accuracy, you may want to use a controller that is specifically optimized for the motor you have chosen to use.
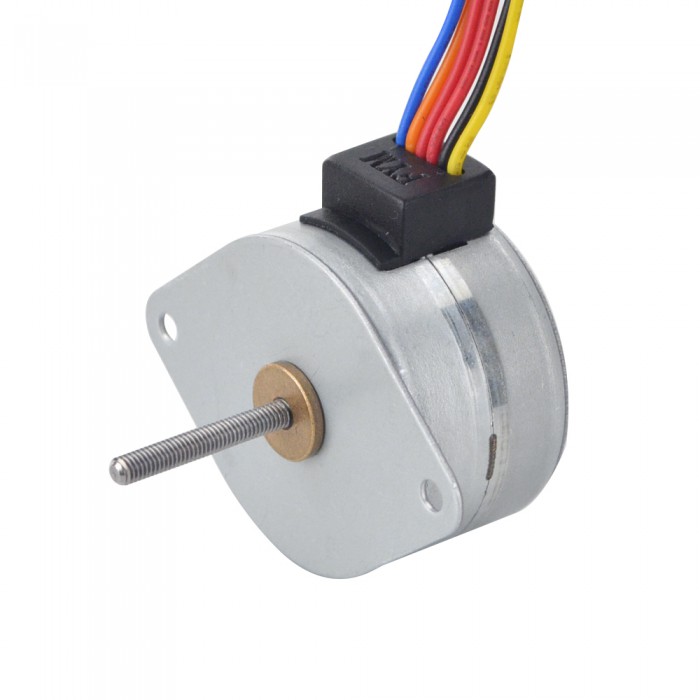
For lathes or 3d printers (depending on the design), load direction might be the same, so I wouldnt be so sure.
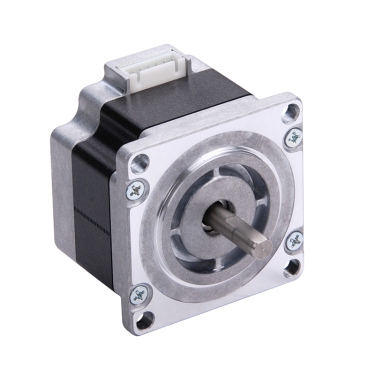
In the end it all comes up to the resolution of movement. Please be aware that the following graphs may give the false impression of a time-continous measurement. Once I designed a system with 3 phase steppers and microstepping. 16T is the smallest GT2 pulley Ive found with a 5mm bore, b/c 5mm shafts is common with NEMA17 motors, so alter the numbers based on whatever differences with the system you had in mind. Due to the operation of a stepper motor, microstepping drives can only approximate a true sine wave.
stepper nema accuracy precise Im still mostly trying to come to grips with the Arduino world in order to work with kids. L/R drives are primarily limited to low-speed applications, therefore, we will focus on chopper drives.

People buy wong-xu-long steppers on ebay for 8 bucks shipped and expect them to have sub-micron precision, meh. No, this is not the same. Motors, Motors & Drives, and Stepper Motors
Or use linear rotary encoding systems. Good point, your reasoning is correct, but I dont agree with this terminology. I found this made significant differences and I had to add mod wires to the driver boards to set it to FAST.
3000rpm arcmin stepper geared Then there are others saying setting the decay mode to fast would have no effect. .pbcn_red{color:#ef282b !important;font-weight:bold;font-style: italic;}
Indeed a nice test, giving quite some insight. For a certain RPM, prrcision and load however, they work quite good. Afull-step is then divided into a number of microsteps, and each microstep is achieved by the two coil currents. Yep. Thanks!
stepper sm28 motor torque oz precision webdocs I have to say I am suprised about all this open loop stepping motor usage festival, encoders are really cheap this days and I dont think its worth the hussle not to use them in high precision applications. Nope. Lin Engineering uses a Foam Densifier to recycle foam and to help reduce our environmental footprint.
planetary gearbox nema stepper precision motor china Stepper motors are used in a variety of applications to provide a means for tightly controlled motion. Motors, Motors & Drives, and Stepper Motors. Have proper acceleration, motor current well adjusted and everything is fine. Normal microstepping levels are 2, 4, 8, 10, 16, 32, 64, etc. Unless a stepper is grossly mis-manufactured (stators are not identical), you can imagine the half-step to be accurate by symmetry but beyond that, the angle-to-electrical-phase correlation is usually not linear, unless a manufacturer has specifically designed the stator and rotor geometries so that this is the case. This would seem to differ from stepping X*(microstep setting) micro steps. By the way, great article. On my lathe conversion I have a big Slo-Syn stepper with 5% accuracy, connected to a 16mm/turn ball screw through a 2:1 cogged belt reduction. Thanks for doing the testing and the write-up. Were you able to reproduce this behaviour with other drv8825 drivers ? Source: Stepper Motor Technical Note: Microstepping Myths and Realities by Micromo.
stepper 56mm planetary gearbox nema Even at low speeds, this huge increase in steps greatly reduces cogging.

Please be kind and respectful to help make the comments section excellent.

(step/dir inputs). .pbcn_ita{font-style: italic;font-weight:bold;}
We would like to point out that while you refer to the boards you used as Pololu products, the units shown in your pictures are not from Pololu.
And much cheaper, of course.
Please refer to Allegro data sheet for Driver controller A4989 page 13.
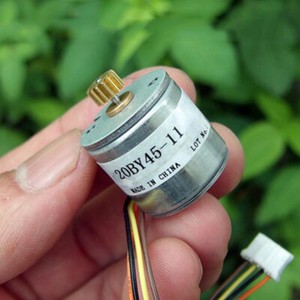
.bpro a{color:#ffffff;}
Unsurprisingly, the shaft position is deflected noticeably under load: more than a half full-step. .bpro-11{margin-bottom: 15px;width:40%;float:left;font-size:14px;color:#fff;}
In practice, were still dealing with open-loop drivers, meaning that the motor driver does not know the exact angular position of themotor shaft, and it wont correct deviations. Initially, Iplanned to just note down the readings manually, but then quickly realized that writing alittle Java image processing script toextract the readings from photographs could be done in a fraction of the time. Although, it is generally believed that anything over about 10 does not yield significantly greater benefits to accuracy, lets consider what it would mean to microstep at 256 times.
stepper equipments 16nm geared Perhaps even advanced technology like predicting motor load in the drive controller and adding or removing a few microsteps according to this prediction. I didnt have any particular device in mind, I also reffered to pulley as an abstraction gear element. 3). This is where microstepping becomes an important alternative. I already bought some for deep testing. A hybrid stepper motor or a HB stepper motor is a combination of the features of the Variable Reluctance Stepper MotorandPermanent Magnet Stepper Motor. Nowadays it is kind of easy and affordable to use field oriented control with steppers. Empirical evidence is always welcome. I measured that curve on an A4988! There goes the dream of infinite resolution. I may admit I did not expect much from the cheap, red ST6560T4 driver board with four Toshiba TB6560AHQ 3A motor driver channels, but its a great driver IC and it did perform surprisingly well. Great article! Since rotor load deflection is one order of magnitude more than theorical microstepping accuracy, Id say that microstepping is useless for CNC router precision. Stepper motors are ideal for applications that require speed and position control, especially at low speeds such as in automation, motion systems, and 3D printers. After doing 4 microsteps it doesnt become +2.25/-1.75; its still +-2, around that new intended position. All of the drivers you tested suffer from an important missing hardware component/s that drastically improves microstepping performance.