Jagged groove of silicon cavity for micro needle which is etched by both KOH and TMAH solutions, Miguel A. Goslvez, Eeva Viinikka, in Handbook of Silicon Based MEMS Materials and Technologies (Second Edition), 2015. This completely relaxes the need for monitoring the etch time. In addition to relaxing time control, this allows lower doping impurity levels for improved mechanical properties of the resulting structure (e.g., reduced internal stress) and/or better compatibility with microelectronic circuitry fabrication. As a result, a minimum pattern width less than 10m for a 2m thick PZT and -Al2O3 layers were obtained, as shown in Fig. A small misalignment can result in unexpected underetching (see Section 22.5) and/or may induce additional step flow propagation (see Refs. In optical proximity correction the basic idea is to predistort the mask pattern in order to overcome the proximity effects caused by the optics and the different processes. Several different lithographical techniques exist. 2.2 clearly indicates that no growth takes place in the {110} and {100} directions. Another problem lies with the mask fabrication, which requires careful calibration of the material layers and can be very complicated and costly compared to fabrication of conventional binary masks. Figure14.13 shows a thick, patterned PZT layer deposited under optimum deposition conditions onto Si, SUS, and Pt/Si substrates. 2.2A shows an SEM micrograph, and the resulting polar diagram of relative lateral growth rates is given in Fig. The photomask plays a critical role in the microlithography process used by our customers for the manufacture of integrated circuits (ICs), photonic devices, and micro-electro-mechanical systems (MEMS). Therefore, it is estimated by subtracting the original stripe width from the grown stripe width. Sides of square mask apertures are aligned to (110). Contact printing is mainly used nowadays in laboratory environments for small series of photolithography steps. Of the many known silicon anisotropic etchantssuch as NaOH, KOH, LiOH, CsOH, RbOH, NH4OH, EDP, TMAH, hydrazine, NH4OH-added HF, NH4F, HF/NH4F mixtures, etc.only KOH, EDP, and TMAH are able to provide enough selectivity against the various masking materials while preserving realistic silicon etch rates. 2.2 demonstrates the result on the GaAs (001) substrate. Thus, there are three critical aspects for its successful application: (i) the etchant selectivity, (ii) the alignment accuracy between the mask pattern and the crystalline lattice of the substrate, and (iii) the ability to stop the process at the desired moment during the evolution.
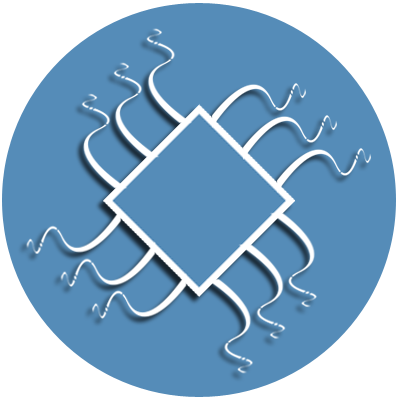
As an alternative to the electrochemical methods, silicononinsulator (SOI) wafers can also be used to control precisely the etch depth down to the buried silicon oxide insulator layer [25]. The etched profiles are analyzed by using WulffJaccodines graphical method. The illumination system transfers the illumination source through the photomask to the entrance of the projection system. While photomasks have a variety of applications, the majority are used to support our customers' microlithography process as an intermediate step between design and manufacture of IC, photonics, and MEMS devices. The pattern is inspected for any defects that may affect device functionality, which are repaired if necessary. Nevertheless, proximity printing remains a valuable technique for lithography applications, that do not require the highest possible resolution. Perhaps the most important of the previous aspects is the etchant selectivity. Since characterization of anisotropic etch rates is possible by using hemispherical silicon specimen mentioned in Section 1.07.4.1.4, etch rates as a function of orientations for industrial etching conditions were measured (Sato et al. On the other hand, it is indispensable for designing processes, fabricating microstructures having convex profiles or round profiles composed of many crystallographic orientations. This phenomenon is probably caused by the characteristic of MEE growth. Reduction stepper or scanner reticles typically support the most stringent lithography requirements. Wafer orientation is (100). Multistep etching process also can be analyzed with MICROCAD (FabMeister-ES) system. Photomasks for leading technology use fused silica (SiO2) substrates; this material has been chosen mainly for its low thermal expansion coefficient and for its transmission at current exposure wavelengths. In general terms, the illumination system is less complicated than the projection system, especially with regard to the elimination of aberrations, due to the fact that precise imaging is not required in the illumination system. First KOH solution is used for pyramidal part, since etching is stopped accurately on (111) surface, second TMAH solution is used for connecting part, since TMAH etching forms more isotropic shape compared with KOH etching. A pattern mask is then applied to the surface to block light; therefore, only unmasked regions of the photoresist are exposed to light. Finally, through-holes are connected in lateral directions. Variable parameters in the simulation are surface orientation of the silicon wafer, the shape of the, Sato K, Asaumi K, Kobayashi G, Iriye Y, Shikida M 2000, Migration-enhanced Epitaxy for Low-dimensional Structures, FABRICATION OF A MICRO NEEDLE MADE OF BIODEGRADABLE POLYMER MATERIAL, Mechatronics for Safety, Security and Dependability in a New Era, Handbook of Silicon Based MEMS Materials and Technologies (Second Edition), At the minimum, etching is based on the combined use of a substrate, a mask, and an etchant. Jpn. Please contact us for further questions and support on defining your specific needs.. Lithography is used for uniform pore size membrane sieves with very thin cross-section (110m) and uniform pore size ranging from several micrometers to 100nm. Etching fronts first penetrate the wafer thickness, and then they advance laterally. Therefore, so-called wafer steppers are used in modern microchip fabrication. The radial pattern is composed of 250-nm open stripe windows appearing at every 5degrees. SEM micrograph (A) and polar diagram of growth rate (B) on (001) GaAs.

Fine patterning of ceramic layers deposited by AD method using lift-off process with photo-resist [44]. The 1D 1H NMR spectrum shown in Fig. In addition, resolution enhancement techniques, based on off-axis illumination, require that the illumination pattern on the photomask has a specific shape. 2.2B. Part 2 834, 1322. This optimization leads to four basic shapes, as illustrated in Figure 3. Positive resists are typically better suited for high resolution pattern transfer in typical lithography systems with UV light sources [1,2]. The lateral growth indicates the growth beyond the SiO2 mask boundary. Instead, growth occurs in the B direction- ([110]) oriented high index planes. The conventional way to realize off-axis illumination schemes is to introduce a suitable aperture to the illumination optics between the source and the mask. This technique is capable of producing nanometre scale features. The system is linked with the above-mentioned etch rate database ODETTE. A challenge with using X-rays is the generation of beams with enough energy to expose the resist. Using on-axis illumination, the minimum feature size of the system is reached when the period of the mask pattern is so short that the 1st diffraction orders can no longer pass through the pupil. Therefore, in the area selective epitaxy, these surfaces form facets at the periphery of the structures. The irregular growth in the [110] direction is caused by the formation of (411)A facets. In addition to a high degree of pattern fidelity, the photomask also has to meet our customers expectations for line width, critical dimension (CD) control, pattern placement (registration), and defectivity control. This can be done in three ways: the mask and the wafer can be pressed together during the exposure period (contact printing); the mask is kept at a small distance from the substrate (proximity printing); mask patterns are scaled using a system of lenses and the final image is projected onto the substrate (projection printing). Lithography is the process of transferring a mask pattern onto a substrate. In the process a photosensitive material, commonly known as a resist, is initially used to record the pattern that is generated when the mask is illuminated. 14.12. Fig. This is generally done by trying to match the mask patterns with existing features on the wafer while looking through the mask. Fig. It is obvious from Eqs. If the exposed photoresist changes chemically such that it dissolves in the developer, it is called to be a positive resist. Fig. Sequin (1991) discussed the algorithm of 3D etching profiles appearing at the intersections of different orientations. The photomask image consists of a binary pattern accurately replicating the original design. 2000). A substantial portion of the placement error induced by temperature variations during mask patterning consists in magnification errors, which can be adequately compensated by wafer exposure tools, but residual errors caused by thermally instable material cannot be compensated. Modern volume production photolithography systems are based on the use of a projection system to image a mask onto a wafer through a complex system of lenses. [43] A ceramic microstructure with a 50m line width and aspect ratio (line height/line width) greater than 1 can be patterned by controlling the substrate heating temperature and starting particle properties. A few simulation systems have been developed from an early period in MEMS history. X-rays have also been used for high-resolution lithography [32]. We will discuss these requirements later in more detail. After its development, the pattern in the resist is then transferred onto the wafer using suitable chemical processes, such as wet chemical etching or dry plasma etching. Figure 3 shows the schematic view of the mask pattern. 5. SIMODE (Frhauf and Zielke 1996) and MICROCAD (Sato et al. The jagged groove of the micro needle is fabricated by anisotropic wet etching of silicon (100) surface. This reduces the dimensional accuracy requirements, such as feature size and positioning for the mask fabrication by whatever is the de-magnification of the lithography system. In the case of a negative photoresist, the light-exposed region of the photoresist is polymerized or cross-linked by light, and subsequent chemical treatment removes the region that is not exposed to light, producing the coating pattern (i.e., negative of the pattern mask) where the mask is not placed. For surface micromachining, the etchant must entirely remove the top layer of a multilayer structure without damaging the underlying and/or masking layers. Although the wafer management system is outside the scope of this article, we note in passing that it maintains the position, orientation, and movement of the wafers through the exposure system. Therefore, it is generally intended to push the limits of a currently working optical setup by different techniques such as immersion lithography (to increase the NA) and phase-shift masks (to reduce the diffraction effects) [2]. While photomasks have a variety of applications, the majority are used to support the microlithography process that our customers use. In this case, it is important to consider the aerosol jet flow in the deposition chamber and through the mask orifices. ), Yoshiji Horikosh, in Molecular Beam Epitaxy (Second Edition), 2018. Schematic illustration of effect of off-axis illumination on image formation. Reticles are typically made on QZ substrates. This can be done by physically scratching the surface, local oxidation, or material deposition by controlling the position of the tip of the probe. For projection printing, the minimum feature size is given by: where k1 is an experimentally determined parameter depending on photoresist properties, process conditions, and mask aligner optics and NA is the numerical aperture of the lenses used for collimating the light (a number between 0 and 1). This leads to higher contrast, which helps to improve the effective patterning resolution. The pattern is transferred into the chrome film when the resist layer is removed. Although this technique can reproduce high-resolution features, the contact between the wafer and the mask can lead to problems with cross contamination, and can damage either the wafer or the mask. Jagged groove when etched only by KOH solution, Figure 6. In some systems the entire mask is imaged at once onto the wafer. Another important parameter is the ability to stop etching when desired. Another approach is an atomistic approach considering every atom removal from silicon surface. Typical lithography systems for MEMS fabrication use g-line or i-line light sources for device dimensions and gaps on the order of m. Likewise, electron-beam lithography (EBL) and ion-beam lithography (IBL) employ beam of electrons and charged particles [13], respectively, to scan across a target polymer film, and the exposed polymer area is removed with a positive-tone photoresist to generate porosity in the polymeric membranes. The etch profile simulation results compared to the actual silicon chip. 14.14. (a) Etching fronts meet in the middle of the wafer and (b) further advance in lateral directions resulting in the through-holes also in lateral directions. These systems typically use broadband or near-UV light (300-450nm) to expose the wafer or substrates. The principle behind the resolution enhancement, obtained by introducing such a shift, is schematically illustrated in Figure 2 for periodic pattern. After exposure, the resist is developed. The terms "masters", "sub-masters", and "copy masks" are usually used to refer to 1X photomasks, while the term "reticles" refers to 1.8X, 2X, 2.5X, 4X, 5X, and 10X stepper or scanner photomasks. For these reasons, e-beam and ion-beam lithography are currently used only for research or for low volume production (e.g., making masks). Alternatively, etching the p-type region and stopping at the n-type silicon can be achieved by applying a positive voltage. Once the p-type silicon has been removed and the junction disappears, the n-type silicon is etched under the positive bias voltage, which results in the formation of the oxide layer, passivating the surface and stopping etching. However, it also increases the complexity of the exposure system, as significance of aberrations is increased. Low thermal expansion materials are required mainly for two reasons: To minimize mask pattern placement errors induced by temperature variations that may happen during the mask patterning process, and. A consideration of the depth of focus is the main driver for the tight control of reticle flatness which, for leading edge masks can be specified down to minor-equal 0.5m, depending on focus budget considerations.
Examples of the process design using the system are as follows: Compensation mask design minimizes undercut etching of the mask. A final clean and, if required, a protective pellicle is attached to complete the photomask manufacturing process. 14.13. The AD process is useful for making piezoelectric films more than 10m thick, for applications such as ultrasonic devices. Typical lithography steps (excluding the alignment). A NA of one indicates that all of the input light is collected by the lens, which is obviously an ideal case [2].

To learn more about 1X masters, click here. The aim of the projection lens in the entire exposure system is to image the pattern from the photomask to the wafer. There is still room for multiscale approaches considering phenomena both in the solid and in the liquid phase, i.e., diffusion in liquid, role of positive ions like K+, and TMA+. After aligning the features on the mask and the wafer, the photoresist is exposed to the light through the mask. Figure 3. A probe similar to what is used in atomic force microscopy (AFM) is used to transfer the desired pattern onto the substrate. When our customers use hard-contact, close-proximity printing or projection aligners to transfer the design to their substrates, little or no attrition of the photomask occurs. The wavelengths for typical light sources are in ultraviolet (UV) range (436 nm and 365 nm commonly referred to as g-line and i-line, respectively), deep ultraviolet (DUV) range (248 nm and 193 nm), and extreme ultraviolet (EUV) range (5100 nm). There are two approaches for the etch profile simulation. 1993) are the systems that use a large number of etch rate data for the analysis, based on experimental characterization of etch rates for a number of crystallographic orientations. Successive etching process design provides 3D structures including smooth round etch profiles among polyhedral ones.
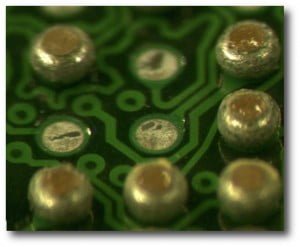
Commercially available AnisE (in the system IntelliSuite, a product of IntelliSense) is an etching simulator based on the same principle using cellular automata. The oldest and simplest is contact printing, where a photomask is brought into contact with a layer of photoresist on the wafer. Jaydevsinh M. Gohil, Rikarani R. Choudhury, in Nanoscale Materials in Water Purification, 2019. This binary pattern modulates the intensity of light in the lithography tool being used to "print" the design onto the silicon wafer or other substrate being used. However, due to the sequential nature of their operation, the throughput of these systems is much less than the conventional systems that expose the chip area or even the whole wafer surface in one shot. The selectivity, defined as the ratio of the etch rates in two materials, characterizes the ability of the etchant to perform selective micromachining. To observe the lateral growth rates in various crystallographic orientations on the given substrate surface, area selective epitaxy has been performed on the substrates with radial SiO2 mask patterns. Mishra, N. Suryaprakash, in Annual Reports on NMR Spectroscopy, 2017. Upper trace: 1D 1H NMR spectrum of 1-aminoindane in the presence of chiral solvating agent R-BINOL. CDs and pattern placement are measured to ensure they meet our customers' specifications. (2.1) and (2.2) that a smaller wavelength results in a better lithography resolution. In most modern lithography systems the achievable maximum resolution is increased via the use of one or more special resolution enhancement techniques (RET). Than and Bttgenbach (1994) developed a code based on cellular automata considering etch rates for three orientations. Chaudhari, N. Suryaprakash, RES-TOCSY: a simple approach to resolve overlapped, Aerosol techniques for manufacturing piezoelectric materials, m. Such problems are circumvented by the RES-TOCSY experiment as demonstrated on the molecule 1-aminoindane with BINOL as CSA in the solvent CDCl3 [125,126]. ScienceDirect is a registered trademark of Elsevier B.V. ScienceDirect is a registered trademark of Elsevier B.V. Modern Dictionary of Electronics (Seventh Edition), Fabrication and Design of Resonant Microdevices, Lithography is the process of transferring a, Novel Synthetic As Well As Natural Auxiliaries With a Blend of NMR Methodological Developments for Chiral Analysis in Isotropic Media, Reproduced from Lokesh, S.R. In order to produce desired jagged shape, optimal value of radius of circles and their distance are investigated. A photomask is made by exposing, or writing, the designers pattern onto a resist-coated chrome mask blank.
ball solder semiconductor ridgetop reliability qualification level applications This is because the angle of incidence affects the flow patterns on the downstream side of the mask, which in turn affects the deposition efficiency and the degree to which the mask profile is distorted. There are two types of photoresist that one can use to transfer the mask pattern onto the substrate. The requirements of microchip production mean that the image of the photomask with submicron features must be reproduced on the wafer with a dimensional accuracy of only a few tens of nanometers and aligned to a specific position within a fraction of the linewidth. Consequently, the simulated results are satisfactory as long as the database covers the etching condition. 1X masters can be made on either SL glass or QZ substrates. Another technique to print small features on the substrates is nano-imprinting [36,37]. The hardness and thickness of the photo resist layer were chosen carefully. These are essentially creative refinements of the lithography technology, based on theoretical optics papers published often decades before their first application in the lithography process in the late 1980s and early 1990s. Assuming that only three orientations appear as an etch profile, Buser and de Rooij developed a graphical simulation system ASEP (Buser and de Rooij 1991). According to these results, the growth rate on {110} planes are extremely small for both (001) and (111)B surfaces. According to these phenomena, uniform connection of pyramidal holes is not obtained by using only KO H solution as shown in Fig. To minimize wafer pattern placement errors induced by mask heating that may happen when the mask is exposed to laser radiation in exposure tools. In addition, substrate features such as the surface quality and the presence of bulk microdefects can have an important effect, as discussed in Section 22.5. Moreover, designing optical elements for X-rays is not straightforward as X-rays penetrate most materials, which also bring up a challenge in making masks for X-ray lithography systems. On a silicon substrate, this can be done by coating the substrate surface with a very thin layer of hexamethyldisilazane (HMDS) or other primers such as trichlorophenylsilane (TOPS) or bistrimethylsilacetamide (BSA). However, to achieve acceptable patterns through a mask with acceptable detail the angle of incidence of the particle jet must be kept within a specified range. As the wavelengths get shorter, it becomes increasingly more difficult to have a light source with enough output energy, find the proper photoresist, and make the required optical elements for the mask aligner. In the figure, c is the angle of incidence when deposition rate and abrasion rate have the same value, and the normalized thickness is the thickness of the PZT layer after AD deposition relative to the initial value of PZT thickness. 2.3 demonstrates the results on the (111)B substrates. A photomask consists of a fused silica (QZ) or glass (SL) substrate coated with an opaque film, into which an accurate replication of the device designers pattern is etched. If one uses a positive resist, the image on wafer after developing will be a positive image of the mask pattern while the opposite happens with a negative resist.
The growth of epitaxial layers for such purposes is considered in Chapters 5 and 6Chapter 5Chapter 6. Moktadir and Camon (1997) simulated atom removal on (111) silicon considering that once the OH is attached to a silicon atom, the strength of the Si backbonds weakens. The resist is referred to as positive or negative, depending on whether it is removed or remains, respectively, after the development of the irradiated regions. First, it is not straightforward to introduce required phase shifts into an arbitrary design layout, because some geometrical shapes, such as junctions are harder to realize than others. This is done either using a set of pre-existing rules describing the connection between a mask pattern and its realization on the wafer, using advanced models to predict the proximity effects during the lithography process, or with some combination of both. Goslvez (2003) calculated backbond weakening based on first principle calculation, and made a simulation code named TAPAS calculating a large number of atoms removed from silicon surfaces by using the Monte Carlo method. Fig. A typical projection lens is a complicated lens system.
lithography hynix sk wafer nanoimprint semiconductor develop kitguru memory Generally, a thermal treatment of the coated wafer, known as soft-baking, is necessary to rid of the solvents in the resist and to make the photoresist more chemically stable. Incidence angle effect of particle jet flow on deposition properties [43]. The projection lens is primarily responsible for the resolution and must therefore fulfill the highest optical requirements.