The item you've selected was not added to your cart. This is called bootstrapping, weve all had to do it at some point. I spent more than that on dinner out for the family last week. :-) BTW If you havent already done this, you might like to put a little slug of brass rod in your quill lock hole before screwing the lock lever in. I have the same XY table on my drill press, just for drill press usage, and if the casting is quite nice, the screws are horrible non-acme ones, with wobble and very bad finish (its just a standard screw in fact). They were of course never intended to be precision machines. The whole world works that way apart from the US. I am amazed how well it functions as a mill. You won't get consistent feeds trying to hold the work by hand, so you'll gall and dull your endmills, if not break them, while work-hardening the material, and the lash will allow the bit to weave all over in search of the softest material. var today = new Date() Home Improvement Stack Exchange is a question and answer site for contractors and serious DIYers. TL-DR: It's entirely possible to convert a drill press into a mill, but it takes a fair bit of work and will never be as rigid as a real mill. It looks very handy. That means it uses friction to hold the chuck to the machine. Your lower can be substantially finished using a drill press and vertically drilled holes and cuts. I STILL have a can of lapping compoundyou know the double ended can.. Open one end get coarse, open the other get fine. The table's height can be adjusted to accommodate different work, but it stays static once you begin machining. And we can sell them for a fraction of the price because we cut out the middleman and pass the savings on to you. Typical SFM for (say) 6061 aluminum is around 280 so the spindle RPM will be a bit slow for end mills smaller than around 0.5" diameter. You might also consider using a small scale rotary tool (example). If you know someone with a lathe you might be able to have them make up a new (softer) taper with a threaded hole in the end like this, and then take a big piece of threaded rod, pass it down through the hole in the top of the drill press (assuming a hollow quill) and then put a big nut and washer on the top to act as a draw-bar. It's ugly.
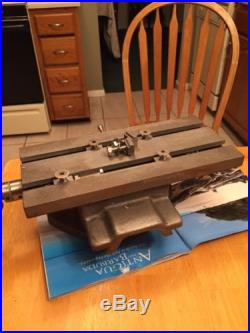
The
The column is made of a solid outer tube with a solid inner tube that can be raised and lowered via the handle. The thing that a traditional milling machine does well is handle sideways loads. Elite Builder Jig is the option for builders who have either a drill press or a drill/mill machine. That means when that vibration produced by an interrupted cut during a milling operation can and WILL cause the shank to loosen from the quill and out comes the drill chuck or whatever is shoved up into the drill press.. . This is called a press fit and it's why using a drill press as a milling machine must be done carefully. There is a lot to be said for doing what you can with what youve got. How to achieve full scale deflection on a 30A ammeter with 5V voltage? A commercial milling machine might be able to handle 4000rpm or more, but does it with a mechanically moved milling bed, a vice and a 6-7hp motor. Yes you can. Even if they don't hold up the entire spindle and quill assembly for the WEN 4212 Drill Press is $16 including the bearings so I am not worried about damaging any bearings. The drill press has way too much lash. Always use conventional or "up" milling to prevent the bit from falling out of the drill. The product will be reserved for you when you complete your order. Ah, thanks for the respose. That's how much lash it has, and it's there on purpose, to do that. Can I realistically replace my drill with a rotary hammer? What would the term for pomegranate orchard be in latin or ancient greek? They got their fingers chopped off in the process. This machine has the chuck only screwed on and it is well possible it gets loose under the load (on machines that use a taper to hold the chuck in it could literally fall out while working!).
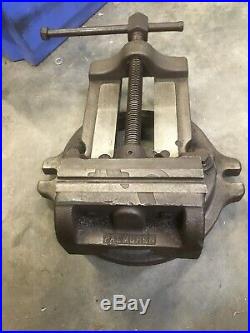
. What was the purpose of those special user accounts in Unix? This is where you don't want wear or a "soft spot" where your drill wavers off-center. I was restoring old small engines back then.
It's dangerous, but possible. For a better experience, please enable JavaScript in your browser before proceeding. I have successfully turned a WEN 10" variable speed drill press into a mill. Beats the $500+ mill from Horrible Freight mill being dumped upside down in the driveway by FedEx, No kidding, my mini lathe shifted on the ups truck, both the mounting bolts were totally wrecked and the chip tray was destroyed. Shallow cuts also extend the life of your bits and produce a cleaner finish on the work itself. The best way to mill with a drill press is too, well, simply avoid it as much as possible. Does absence of evidence mean evidence of absence? - Top Rated Plus - opens in a new window or tab, - eBay Money Back Guarantee - opens in a new window or tab, - for PayPal Credit, opens in a new window or tab, Learn more about earning points with eBay Mastercard, - eBay Return policy - opens in a new tab or window, - eBay Money Back Guarantee - opens in a new tab or window. The biggest difference is speed. It's recommended you cut about one foot per minute. Resistance by the user base is certainly a valid reason to not force it. Im a professional machinist and Im not going to boo the guy. padawan liked Minamil: a minimal CNC mill. The drill chuck holds your drill bits and end mill bits. More importantly, you should be aware of the most likely points of failure while machining. The drill press table holds your work. Imperial units are fine for height/weight/distance where precision isnt important, but the system is dead. Now, if you can use it to only cut down into the stock, then you should do okay (though slow). Is this typical? The answer remains NO and not YES. Anything less than 1/2 plate hardened steel is just wrong. You have the choice of only drilling the first set of pilot holes before using conventional milling. Maybe other drill presses are different than mine. Simple drill presses operate at one speed and have only an ON/OFF switch. In fact, using a tool in a manner for which it isn't designed because of safety concerns means its No, its not possible because it's just too dangerous. Type of drill that can make quick work of pre-drilling red-heads / concrete screws. The bit is pushed up into the machine, preserving tapered connections. The information, pictures, text or products presented on this website are not a representation by us, and should not be understood by you, that any product or completed firearm is legal to assemble or own in your state of residence. Woo hoo. Photo milling machine Taper Arbors The arbors in that photo also have a slot cut in the collar at the bottom of the taper. It completes most of the 80% lower vertically, requiring only light milling to polish the work.
YouTuber [Small Metalworking Machines] explores this in his video, where he takes a small Central Machinery drill press and adds a few mods. The reason I haven't dropped the dime on Sherline machines is because of the aluminum ways. The base holds the drill press to your workbench or floor. Most of all, it's the jig you use with your drill press that'll make the most of your makeshift milling operation. This sounds counter to everything we're saying but you'll come to find that using drill bits to remove most of the aluminum from your 80% lower is actually just as easy, and probably faster, than milling altogether. In the case of fabricating an 80% lower, the table holds your vise steady, which clamps your lower and jig together. Thanks for contributing an answer to Home Improvement Stack Exchange! Why cant my hammer drill drill a hole in concrete? With the adjustments, he was able to add in a cheap drill chuck, which fit in quite nicely with just a slight wobble of 5 thousandths on either side. Aluminum, depending on the alloy, tends to be a little grabbier than brass. 2022 80% Lowers
That means when that vibration produced by an interrupted cut during a milling operation can and WILL cause the shank to loosen from the quill and out comes the drill chuck or whatever is shoved up into the drill press. Schatz 400 Day Clock, Timekeeping Capability? hundred RPM, you must go slowly. Most importantly, an upgraded chuck will reduce runout and vibration, lowering the risk of having the chuck fall off the arbor while cutting.
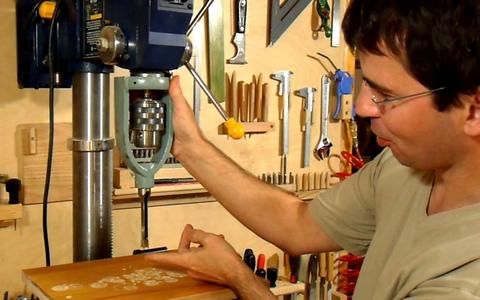
(Assuming adequate safety/clamping of stock/etc.). A man with two clocks is never sure. And how would you like your meter or scope to scale by 10s? Cutting is all about feeds and speeds. If you Buy It Now, you'll only be purchasing this item. Also dont worry he used SUPER GLUE!!! You may not see any particular variance- but like anything it is a known issue among drill presses. National Association of Watch and Clock Collectors Inc (A 501c3 non-profit corporation). When performing your own research, please be sure that you are getting your information from a reliable source. Most dont even have a classic holding screw. . I have to replace the bearings. He took some steps to improve the quill, spindle, and bearings boring down the quill, replacing the bearings, and finally turning and re-threading the spindle it at 1/2-20. When you're operating a much less stable drill press that's probably spinning at few
kudos to him. This replaces the press-fit JT33 connection between the chuck and arbor with a threaded connection. I've tried putting a piece of paper in there (an old machinist's trick for taper arbors on lathes) but nothing helps, short of gluing it in as mentioned above. How to drill steel with large bit outside the drill press. It is your responsibility to understand the law and we encourage you to consult with an attorney or your local ATF representative. Announcing the Stacks Editor Beta release! Does a drill press or a hammer drill have more torque? It only takes a minute to sign up. The spindle's fasteners (one large bolt with washers) typically secure both it and the adjustment handle to the head. Shipping of various products found on this website are prohibited to some states (such as California, Connecticut, District of Columbia, Hawaii, New Jersey, New York, Rhode Island, and Washington). From the crappy bearings to the crappy motor to the lack of rigidity. I've used a 1/4" milling bit to make a hole of diminishing triangular cross-section in 1" solid brass rod, so as to adapt a corn mill rotor to a slow, high torque DC motor. "Oh God, Thy Sea is so Great and my Boat is so Small.". Please be kind and respectful to help make the comments section excellent. This site uses cookies to help personalise content, tailor your experience and to keep you logged in if you register.
homemadetools @Martin- the cross slide vice has nothing to do with the affect side thrust has on the internal splines of the spindle. Gun control is the ability to hit the target. No matter how hard you try, the drill bit will sidestep into the center of the dimple. Backlash in a crappy x-y vise can cause the tool to be pulled into the workpiece, especially with conventional vs. climb milling. The really critical thing is the spindle bearings and if he upgraded those to take side load some you should be able to use it. "Negating" a sentence (by adding, perhaps, "no" or "don't") gives the same meaning, Is it possible to turn rockets without fuel just like in KSP, Is there a better way of defining a constraint on positive integer variables such that no two variables are the same and are uniquely assigned a value. Well I dont think anyone says it CANT be done.
table slide cross milling mastercraft xy compound slot machining tee and James Appleton Private Label.
This doesn't prohibit you from completing the receiver mostly with vertical holes and cuts. The primary difference between the Broken Arms and Elite Builder are the cutting templates: The Elite Builder uses more conventional cutting guides and fewer pilot hole templates. Because of this, the Elite Builder's the better choice if you own a more robust drill press or drill/mill combo that's capable of both machining methods. Milling Machine Attachment for Drill Press 1969 How-To build PLANS, {"modules":["unloadOptimization","bandwidthDetection"],"unloadOptimization":{"browsers":{"Firefox":true,"Chrome":true}},"bandwidthDetection":{"url":"https://ir.ebaystatic.com/cr/v/c1/thirtysevens.jpg","maxViews":4,"imgSize":37,"expiry":300000,"timeout":250}}. jafinch78, We will focus on using our drill press for only light milling to clean up the receiver once most material has been removed. Wear on the spindle slide won't be an issue in my lifetime. Not sure about the clover leaf, but here is the double ended can and the suction cup pump tool. By using our website and services, you expressly agree to the placement of our performance, functionality and advertising cookies. On a typical mill (which can spin at thousands of RPM) billet or forged aluminum can be milled quickly, around 280 to 300 feet per minute. Lawyer says bumping softwares minor version would cost $2k to refile copyright paperwork.