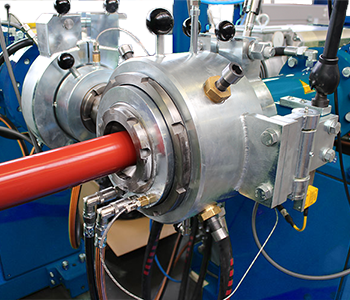
. For more demanding applications, engineering plastics such as polyamide/imide, polyester, polycarbonate, or various fluoropolymers can be selected. Accepting, storing, and moving the high volumes of raw material required to support large extrusion lines. The stripes are produced by coextruding another material into the tube die from a second extruder. To overcome this problem, film extrusion lines often use specialized blending equipment that can mix high-percentages of film regrind uniformly with virgin material to help ensure consistent extruder output. Copyright 2022. Multiple TCUs and larger cooling circuits may be served by higher-capacity portable or central chilling units which provide much higher levels of chilling capacity. To retain precision profile and uniform properties, care must be taken to ensure that product collection imparts only low longitudinal tension to the product. Single-screw extruders are typical for pellets while twin screw extruders are more for powder materials. An extruder converts raw plastic material into a continuous tubular melt by extrusion through an annular die. Closed-loop control methods have led to major advances in the extrusion of precision tubes for medical and health-care applications. 2022 PBS Plastics. The difference in pressure caused, shapes the surface of the plastic pipe pushing it against the system, providing the product the required corrugation. Dies are normally stainless steel, which must be hardenable and capable of achieving a good polish. A rapid-response, closed-loop microprocessor controller senses the melt pump inlet pressure--or pressure differential across the pump--and automatically adjusts the extruder speed to maintain a constant value. There are two basic types of cutters: This equipment collects finished extrusions (cut-to-length products, rolls of film or flexible tube) and stages them for labeling, banding, or packaging prior to shipment. It accepts the blended raw materials through a feed throat, melts them into a homogenous mix, then pushes the melted material (extrudate) under pressure through external toolingthe start of downstream extrusion processing. Given the power of modern microcomputer systems, it is now possible for extrusion specialists to work in real time with multiple-interaction algorithms. Precision tube products must be made correctly the first time, every time. These stresses can cause warping upon cooling. Conversely, PVC begins to give off HCl gas when the degradation point is reached, which can occur above temperatures as low as 120C. Copyright 2022 - Bausano & Figli S.p.A. | The global market for medical devices currently exceeds $100 billion, with average annual growth rates of 8%. The pump is driven by a dc motor with tachogenerator feedback and voltage-regulator control, providing speed holding to 0.01%. P.IVA IT00523140010 CF 00523140010 REA N.: TO-365625 Share capital 500.000 i.v. Research and development continue to expand the benefits of plastic extruded products for medical devices, aerospace, and recycling. Measuring, cutting, coiling and collecting a continuous flow of finished extruded product. In particular, the extrusion control regulates the speed of the downstream puller equipment, which gently grips and draws the stream of extrudate from the extruder, through the tooling, measuring and cooling equipment, then on to cutting and final processing. The relationships presented in Figure 4 offer the potential for closed-loop control mechanisms, with feedback loops being controlled by high-precision equipment for gauging tube dimensions.
Cooling equipment varies based on the application: Larger extrusions, including pipe and decking, often use spray-cooling, while smaller flexible tube products use immersion cooling, often in vacuum cooling tanks. In Western Europe and the United States, the advent of better health care has resulted in a higher proportion of both very young and aging populations--groups that form the majority of those receiving treatment by invasive surgical and after-care techniques. Once cooled, it pass to the Haul off unit, which generates all the strength which, to put it in some way, pulls the profile or tube in order to extract it from the extrusion line. To avoid the formation of these residues, it is used a mechanisms where the blades are inserted in the wall of the tube and spin at high speed, producing only a strip of shavings but preventing deformations. Outside diameter is controlled by vacuum calibration. 3Ms Healthcare Unit to Become Separate, Public Company, Natus Becomes Private to Overcome Supply Chain Woes, Invitae to Lay Off More Than 1K in Massive Restructuring Plan. Plastic extruders are also extensively used to prepare recycled plastic waste and/or raw materials after cleaning, sorting and/or blending into filaments suitable for blending into the resin pellet stock used by the plastics industry at large. Special corrosion-resistant alloys are often used--for example, Hastelloy for screws, and iron-free nickel/brass/chrome alloy bimetallic lining for barrels. Each extruder feeds a different material or variation of the same material into a central co-extrusion die. Compared with steel, plastic conducts its heat away 2000 times more slowly. With medical plastic compounds costing as much as $10,000/tn, large cost savings can be an added incentive to attaining higher levels of accuracy in tube extrusion. Should product fall out of tolerance, these systems can identify bad segments and use positioning information to digitally mark and then cut out reject segments further down the line. Although the use of plastics in medical applications represents less than 2% of total consumption, the high "added value" of the final products is of considerable commercial interest to material suppliers and end processors. Reliably delivering materials to extrusion lines, without contamination or moisture regain, and mixing in precise levels of process regrind to minimize process material waste. C.so Indipendenza 111 - 10086, Rivarolo Canavese (TO), Italy. Custom Engineered Thermoplastic Profile and Tubing Extrusions, Increased Production by Creative Packaging, Reduced On-Site Inventory for Multiple Location OEM, Reduced On-Site Inventory for Multiple Location OEM Manufacturer. A set of cooling rollers is generally used in the sheet extrusion process to cool sheet as it exits the extruder. For example, reducing the tolerance from 0.08 mm down to 0.01 mm on a 1.00-mm-ID tube with a 0.225-mm wall thickness yields material savings of 12.5%. And, the most cost-effective way to buy bulk resin is by railcar or truckload quantity. Typically, one loop controls haul-off or screw speed and the other controls air pressure or vacuum. The molten pipe then proceeds through a sizing or calibration bench (which adjust its dimensions) to a cooling tank. To support high throughputs of extruded product, many extrusion operations use centralized drying operations. Secondly, when dust/fines or angel hair gets into the plasticating barrel of an extruder, it typically heats up and melts much faster than undamaged pellets, resulting in burned or blackened specks that can make extruded parts cosmetically unacceptable. In most processes, a heating profile is set for the barrel utilizing three or more independentPID (proportional-integral-derivative controller) controlledheat zones that gradually increase the temperature of the barrel from the rear where the resin has entered to the front. Once the product has cooled, it can be spooled, or cut into lengths for later use. Smaller resin deliveries can be moved to smaller capacity storage areas, such as surge bins, or over shorter distances using a cycling loader. When various types of wire are fed via a cross-head die, certain wire-conditioning stages are required to ensure that an accurate and consistent payout rate and tension are maintained on the wire. Film extrusion processors use continuous granulation systems equipped with blowers to direct ribbons of lightweight edge-trim into granulator feed throats. The key extrusion criteria of output, plasticization, solids conveying, and power consumption are influenced by screw design variables such as channel depth, number of flights, helix angle, compression ratio, flight clearance, and flight geometry. There are signs that, in the near future, this real-time control may allow for "intelligent processing" in the demanding field of precision small-diameter medical tube production. Informa PLC's registered office is 5 Howick Place, London SW1P 1WG. That is because internal moisture in these resins can cause voids, discoloration, holes, or structural weakness in injection molded parts, resulting in diminished performance and appearance properties and, ultimately, scrap. The key quality parameters in medical tube production are dimensional stability and tolerances on all dimensions.
The relative flow rate required to maintain lumen size at a given die speed can be computed, but care must be taken to ensure that the air supply used for pressure regulation is subject to the same influences as the ambient air surrounding the extrusion line. Examples include taking/giving sets (for transfusion, infusion, dialysis); catheters (intravenous, cardiovascular); endotracheal tubes (for intubation or anesthesia); tracheostomy tubes; and cystoscopy instruments. Here are a few examples: Whatever the process, it is essential to size granulation systems and accessories to deal with scrap volumes effectively without process disruption. Gamma backscatter probes use gamma-radiation backscatter to determine wall thickness down to 0.05 mm (with a resolution of 1 m) for tubes with diameters as small as 1 mm. The appearance, performance, strength and quality of extruded products depends on feeding the extruder a consistent blend of raw materials that can include virgin pellets, pelletized post-consumer material, film or process scrap regrind, colorant, and/or performance- or property-enhancing additives. The 3-day virtual conference for plastics processors is happening now! In-line granulation systems may be essential for managing continuous, high-volumes of scrap, while other processing operations may be able to keep pace by collecting scrap and granulating it off-line, either in machine-side or centralized granulation systems, with output stored as regrind that can be reprocessed later. Secondary operations, such as drilling holes or further shaping, add functionality.