S1359431117309353. However, these subjects are beyond the scope of this article. 102, 158166. Its operation depends on the ability of the working fluid to achieve high enough vapor pressure when heated to push the liquid condensate back to the evaporator section of the device. J. Therm. Early versions of this device (not shown) were typically a planar rectangular shape that are comprised of a lower plate into which a series of interconnected pathways are machined, and smooth upper plate that gets bonded to the lower one, air and working fluid. Operational Limit of Closed Loop Pulsating Heat Pipes. Lin et al. After the condenser section, the tube narrows as the size required for the liquid is quite a bit smaller than required for the vapor. OHP Heat SinksOHP Heat SpreadersOHP Thermal StrapsVapor Chambers + Wick-Based Heat PipesCold PlatesEjector RefrigeratorsDesign Services, NewsExperienceCertificationsVendor Terms & ConditionsBURNOUT Mug, CCA Heat Sinks Embedded with Oscillating Heat Pipes, Air Force, small business develop technologies that help electronics stay cool, AIAA Thermophysics video of Neutron Imaging based visualization of an Oscillating Heat Pipe in operation carrying 400W. Numerical simulation studies show that the CPU temperature is negatively correlated with heating power and axial fan pressure, and positively correlated with cooling air temperature.
oscillating pipe heat Where, l, , hlv and l represent working fluid density, surface tension, latent heat of vaporization and dynamic viscosity, respectively. 2. Typical operating temperatures for ammonia-based loop heat pipes are between -40 and 70 deg C. Generally, we see this type of device in space-related applications. PHP has unique advantages in solving heat dissipation because of its compact structure and high heat transfer coefficient, which has attracted much attention from scholars (Zuo et al., 1999). Heat-generating devices in the server that is the basic component of a data center mainly include processors, storage units, voltage regulators, chips and power supply equipment. Eng. Continuous influx of new bubbles at the lower part of the liquid plug causes the pressure difference at both ends of the liquid plugs to increase, which pushes the high-temperature liquid plugs of the evaporator to move to the condenser. (A) Thermal resistance and (B) average temperature in the evaporation section with different wind speeds for the PHP CPU cooler (Shang et al., 2021). In contrast to a conventional heat pipe, there is no additional capillary structure inside the tube. Cramming More Components onto Integrated Circuits. Extremely high effective thermal conductivity [even thousands of times higher than that of copper rods (El-Nasr and El-Haggar, 1996)], low effective thermal resistance and the feature of no moving parts make it a promising cooling method for electronic devices such as computers, telecommunications and satellite modules. Therm. Since there are no any moving parts, no additional energy is needed, which will make the PUE value infinitely close to 1, achieving extremely high energy efficiency. Int. (A) The overall view and (B) internal view of the enclosed rack heat dissipation system based on PHP, and (C) the CPU temperature variation under different rack heat loads (Chao et al., 2017). The hot end overheating leads to secondary heat dissipation difficulties, the cold end undercooling leads to CPU chip surface condensation affects its performance and life, and the manufacturing cost is too high, which also restricts the large-scale application of thermoelectric refrigeration technology. The results show that the PHP-based radiator can reduce the junction temperature by 45C compared with the traditional thermal thermosyphon radiator, which will help heat dissipation inside the rack. (2013) showed that larger surface tension will increase the critical value of the pipe diameter, and increasing the pipe diameter will reduce the flow resistance, which can improve heat transfer performance. Focused on Thermal Management, TIMs, Fans, Heat Sinks, CFD Software, LEDs/Lighting, May 1, 2003 Sameer Khandekar Heat Pipes Design, liquid cooling, Number 2, PHP, Pulsating Heat Pipe, Volume 9. Eng. As the names suggest, in a closed loop structure, the tube is joined end-to-end (Figure 1b). Experimental Investigation of Flat Plate Closed Loop Pulsating Heat Pipe. Our team of scientists and engineers have published many OHP resources. Sensible/latent heat are both heat transfer mechanisms of PHPs, but their respective proportions have not yet been fully understood. Meanwhile, liquid cooling faces the problem of precise control of sensitively responding to changes in the heat generated by the cabinet and timely adjusting the cooling capacity and flow. Pulsating Heat Pipes: Progress and Prospects, in Energy and the Environment - Proceedings of the International Conference on Energy and the Environment. Appl. Great achievements have been made in the research and development of pulsating heat pipes, but there are still many urgent problems to be solved and further exploration is needed, which are summarized as follows: 1) Operating mechanism. Heat Transfer 21 (2), 405409. This design makes them a much better heat spreader and perfect for applications where a high degree of isothermality is required. The authors declare that the research was conducted in the absence of any commercial or financial relationships that could be construed as a potential conflict of interest. Energ. Int. In addition to this, studies on the mixing surface (hydrophilic in the evaporator and hydrophobic in the condenser) have shown that the unidirectional flow of working fluids in PHPs can improve its performance (Hao T. et al., 2014, Hao Tingting et al., 2014; Leu and Wu, 2017). Topics include new methods in liquid cooling, unique TIMs, connector selection, and much more. doi:10.1016/S1359-4311(03)00168-6, Khandekar, S., Dollinger, N., and Groll, M. (2003b). Thus, a self-sustained thermally driven oscillating flow is obtained in a PHP. J. Mech.

However, different scholars have reached conflicting conclusions about whether higher or lower surface tension values are more beneficial to PHPs performance.

31 (2), 622638. As Celsia has numerous website pages on this subject (see below), we wont do a deep dive here. Compared to solid metal fins, this type of fin structure is certainly light weight. Analysis of Chaotic Flow in a 2D Multi-Turn Closed-Loop Pulsating Heat Pipe. In Situ investigation of Liquid Films in Pulsating Heat Pipe. The presence of an approximately triangular or saw-tooth alternating component of pressure drop superimposed on the average pressure gradient in a capillary slug flow due to the presence of vapor bubbles. Since PHPs are usually made of copper, aluminum or silicon, Table 1 summarizes the types of working fluids that are compatible with copper/aluminum/Si PHPs between 0 and 100C. To be sure, the heat exchange effect is best when all the heat in the evaporation section can be dissipated through the condensation section. The smaller the value, the smaller the power consumption and the higher the energy utilization rate. Based on the introduction of the basic structure, working mechanism and outstanding advantages of pulsating heat pipes, this paper reviews in detail the researches on the factors affecting its performance, so as to evaluate the possibility of using pulsating heat pipes in data centers. The hydrophobicity of the condensation section of PHPs will reduce the fluid resistance, making the fluid of PHPs easier to move, and the pulsation amplitude is larger. FIGURE 8. Experimental Investigation on the Effect of the Condenser Length on the thermal Performance of a Micro Pulsating Heat Pipe, in Applied Thermal Engineering Design Processes Equipment Economics. Some common conclusions can be referred when designing a PHP cooler for high power electronic chips, e.g., the higher number of turns will aid in high heat load dissipation and tilt angle insensitivity; self-rewetting fluid is preferred; the optimal charging ratio is around 4050%; the hydraulic diameter of tube commonly selected is around 12mm, et al. Miyazaki (2005) designed straight and finned flexible PHPs to study PC CPU heat dissipation. Servers are an important component of data centers, but they are also the main power consumers. In addition, PHPs have an edge over conventional wicked heat pipes as they are not limited by capillary or entrainment performance limits encountered in conventional heat pipes. 119, 110201. doi:10.1016/j.expthermflusci.2020.110201, Hu, C., and Jia, L. (2011). It can be seen that the development of high-efficiency cooling technology is of great significance, whether it is, to ensure the safe and efficient operation of electronic devices, or to save power in the data center and improve the level of energy utilization. Int. (2001) was used to simulate the vapor slugs and liquid plugs behavior in 2-turns closed-loop and open-loop PHPs. The rack level cooling system can realize the direct cooling of the IT equipment in the rack, and determine the amount of cold air by changing the fan speed and adjusting the location of the server to optimize the flow channel. Heat Mass Transfer 55 (21-22), 61096120. A PHP is a complex heat transfer device with a strong thermo-hydraulic coupling governing its performance. Moreover, the mature commercial system of PHPs has not been fully established, and the lack of theoretical guidance in the practical application process cannot ensure the safety and stability of PHPs. Effects of the Evaporator and Condenser Length on the Performance of Pulsating Heat Pipes. Structure of a Heat Pipe. Int. A survey report published a few days ago in Science magazine pointed out that the power consumption of data centers in 2018 was approximate 205TWh, accounting for about 1% of all power consumption in the world, and the total power consumption still increase by 6% annually (Masanet et al., 2020). The experimental study conducted by Yang et al. doi:10.1016/j.apenergy.2017.08.037, Han, X., Wang, X., Zheng, H., Xu, X., and Chen, G. (2016). Groll, M. and Khandekar, S., Pulsating Heat Pipes: A Challenge and Still Unsolved Problem in Heat Pipe Science, Proceedings 3rd International Conference on Transport Phenomenon in Multiphase Systems, ISBN 83-88906-03-8, Kielce, Poland, 2002, pp. CL: Investigation, formal analysis, writing original draft. With the increase of heat flow density, bubbles are formed on the solid surface. The liquid can return to the evaporator in time, and the heat transfer performance is improved. (2008) showed that the 2mm closed-loop PHP has the best thermal performance when the inclination angle is 90, but the thermal performance will no longer be related to the inclination angle when the pipe diameter is reduced to 1mm. The total power per server can reach 300800W, and the power of a single rack can reach 2030KW. doi:10.1016/S1872-5813(07)60034-6.
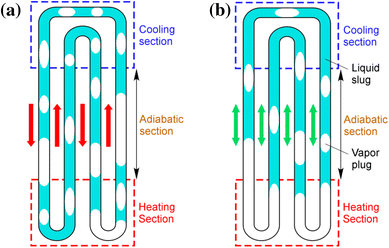
Here, at the upper bounds of temperature, working fluid vapor pressure is high enough to push all the NCG to the extreme end of the heat pipe, beyond the condenser region. doi:10.1016/j.applthermaleng.2007.10.019, Lin, Z., Wang, S., Zhang, W., Lee, E., Zeng, X., and Tang, Y. Masanet, E., Shehabi, A., Lei, N., Smith, S., and Koomey, J. The designed PHP thermal resistance is 0.2C/W in the case of horizontal placement, which can meet the heat dissipation requirements of 1250W/cm2 chips. Int. A Review on Efficient thermal Management of Air- and Liquid-Cooled Data Centers: From Chip to the Cooling System. The established mathematical and physical models have made many assumptions and simplifications, so that the calculated results are quite different from the actual results. doi:10.1016/j.ijheatmasstransfer.2012.05.068, Daraghmeh, H. M., and Wang, C.-C. (2017). However, it is out of the scope of this review. In terms of heat dissipation, high thermal conductivity interface materials and other advanced thermal management methods can be used for heat dissipation. Therefore, the length of the condensation section can be designed to be greater than the length of the evaporation section. Filling rate refers to the ratio of the working fluid to the effective volume in the tube. The research on its heat transfer performance will be further elaborated in the subsequent articles. All Rights Reserved.Privacy Policy | Cookie Policy. Amsterdam, Netherlands: Applied Thermal Engineering. The first uses a traditional manufacturing method where two stamped copper plates are bonded together, complete with wick structure, working fluid, and the addition of a support structure. At this time, the PHP deviates from the vertical position, and the shape of the bubble is asymmetrical along the pipe axis to form a convex portion, which accelerates the movement of the bubble. Effect of Using Ethanol and Methanol on thermal Performance of a Closed Loop Pulsating Heat Pipe (CLPHP) with Different Filling Ratios, in INTERNATIONAL CONFERENCE ON MECHANICAL ENGINEERING: Proceedings of the 11th International Conference on Mechanical Engineerin. Jo et al. Heat Mass Transfer 55 (2122), 57225728. J. Azar, K., The History of Power Dissipation, ElectronicsCooling, Vol.6, No.1, January 2000. Its structure consists of three parts along the axial direction, including evaporator, adiabatic zone and condenser. Nevertheless, the prospects are too promising to be ignored. (2021) developed a PHP-based CPU cooler and carried out experimental research on it, as shown in Figure 10. 1, some cavities on the inner surface of the capillary will form new microbubbles in the liquid plugs. Yang et al. J. E3S Web of Conferences 67. doi:10.1051/e3sconf/20186703035, Borgmeyer, B., and Ma, H. (2012). Through the vapor-liquid phase change, abundant heat can be transferred at both ends, and the pressure drop is small, which is isothermal. Int.
oscillating 17-28.). A Novel Thermal Module with 3-D Configuration Pulsating Heat Pipe for High-Flux Applications. Appl. Therm. doi:10.4236/jectc.2013.31004, Wang, J., Ma, H., Zhu, Q., Dong, Y., and Yue, K. (2016). Convers. Moreover, for the purpose of achieving the unidirectional flow of working fluids, closed-loop PHPs with check valves are introduced (Han et al., 2016). Exp. Khandekar, S., Groll, M., Charoensawan, P., and Terdtoon, P., Pulsating Heat Pipes: Thermo-fluidic Characteristics and Comparative Study with Single-Phase Thermosyphon, Proceedings 12th International Heat Transfer Conference, ISBN-2-84299-307-1, Grenoble, France, 2002, pp. Tong, B., Wong, T. and Ooi, K., Closed-Loop Pulsating Heat Pipe, Applied Thermal Engineering, ISSN 1359-4311, Vol.

J. Aprianingsih, N., Winarta, A., Ariantara, B., Putra, N., Kusrini, E., Juwono, F. H., et al. doi:10.1016/j.ijheatmasstransfer.2017.04.112, Yang, H., Khandekar, S., and Groll, M. (2008). Although statistics show that the optimal filling rate range is 0.350.65 (Han et al., 2016), the optimal filling rate is affected by other factors such as the physical properties of the working fluid, the inclination angle, the pipe diameter, and the input heat load, which cannot be uniformly defined. Effects of Geometry and Multisource Heat Input on Flow and Heat Transfer in Single Closed-Loop Pulsating Heat Pipe.
oscillating 23/4, 2002, pp. Fluid Sci. doi:10.1007/s00231-011-0882-9, Sakanova, A., Alimohammadi, S., Mcevoy, J., Battaglioli, S., and Persoons, T. (2019). Typical pressure-enthalpy diagram.In this way a sustained non-equilibrium state exists between the driving thermal potentials and the natural causality, which tries to equalize the pressure in the system. Compared with the traditional heat pipe, the coreless design of PHP greatly reduces the capital cost of the manufacturing process, and the self-excited oscillation pulsation makes the heat transfer performance higher and the heat transfer distance longer, which has great application potential in the high-power data center. Jung, C., and Kim, S. J. Tseng et al. However, according to the authors knowledge, there are few research reports on the application of PHPs in data center thermal management so far. FIGURE 12.

Influence of Filling Ratio and Working Fluid Thermal Properties on Starting up and Heat Transferring Performance of Closed Loop Plate Oscillating Heat Pipe with Parallel Channels. In addition to this startup, there is also a startup process induced by nucleation in the PHPs. Under a maximum thermal load of 100W, its thermal resistance is nearly 0.28K/W, which can keep the temperature of the CPU thermal simulator at about 75C level. (2016) found that the startup time of PHPs decreased with the increase of heating power, and this was verified in Patel and Mehta (2017) on the startup mechanism of PHPs. (2015) showed that methanol as a working fluid is often used under high heat load input conditions, showing a better heat transfer performance than ethanol in a wide range of heat load, while ethanol is more suitable for lower heat input. J. Therm. Heat Mass Transfer 77 (oct), 834842. Figure 9 depicts that the heat source temperature of the aluminum finned radiator is higher than the limited temperature of CPU (70C), reaching 81.6C when the input power is 80W. While the heat source temperature value of the vertical radiator is 64.3C, and the temperature distribution is more uniform, showing excellent heat dissipation performance. Verma, B., Yadav, V. L., and Srivastava, K. K. (2013). Their complex operational behavior, which is not yet fully understood, has raised an ever growing academic interest. Table 3 summarizes the researches on heat dissipation of CPU and high-power devices based on PHPs, and the total thermal resistance variations with input powers from different researches are plotted in Figure 12, which is also compared with the required thermal resistance for CPU cooling (red solid line). Therm. The thermal performance of PHPs will indeed be improved to a certain extent, but it also increases manufacturing and maintenance costs accordingly. doi:10.1016/j.rser.2015.12.350, Hao, T., Ma, X., Lan, Z., Li, N., Zhao, Y., and Ma, H. (2014b). J. Therm. Int. IEEE 86 (1), 8285. 102, 7888. A Review of Data center Cooling Technology, Operating Conditions and the Corresponding Low-Grade Waste Heat Recovery Opportunities. 208-217. When the working fluid is gradually heated at the evaporator to meet the minimum superheat required for bubbles generation, the continuous growth and combination of bubbles will cut off the long liquid plug to generate new liquid plugs and vapor slugs.

Two designs depicted in a single image. Start-up, Heat Transfer and Flow Characteristics of Silicon-Based Micro Pulsating Heat Pipes. Wang X. H. et al. Tech. The critical research results of many scholars on its influencing factors are summarized in Table 2. Fluid Sci. Washington, D.C.New York: Hemisphere Publishing Corp.McGraw-Hill Book Co., 256. J. Appl. Denucleation initiated by liquid film evaporation is more likely to occur in heat pipes with low filling rate and relatively uniform vapor-liquid plug distribution, while the nucleation start is a necessary way for the PHP to enter full-scale oscillation, especially for a high filling rate. 4) The thin liquid film formed by the movement of the liquid plug can significantly enhance the heat transfer of evaporation and condensation. All claims expressed in this article are solely those of the authors and do not necessarily represent those of their affiliated organizations, or those of the publisher, the editors and the reviewers. 28 (1), 4959. Therm. This work is supported by National Natural Science Foundation of China (Project No. However, a working fluid cannot have all the best physical properties required, which can only be the result of a balance of these physical properties. On this basis, every 2C increase in temperature will reduce its reliability by 10% (Haywood et al., 2015), which will bring huge challenges to the electronic information technology industry. FIGURE 5. Multi-objective Layout Optimization of a Generic Hybrid-Cooled Data centre Blade Server. Unfortunately, this cant usually be done with water as the working fluid. doi:10.1016/j.expthermflusci.2014.02.007. The operating mechanism in the PHPs is relatively complicated, and the degree of understanding of it is still insufficient. Appl. J. The performance success of the device primarily depends on the continuous maintenance or sustenance of these non-equilibrium conditions within the system. doi:10.1016/j.ijheatmasstransfer.2014.12.010, Xiahou, G., Zhang, J., Ma, R., and Liu, Y. (2021). Appl. Compared with pure working fluid, the reason why the performance of binary mixed fluid is better can be explained by the characteristics of phase change and intermolecular momentum exchange of mixed fluid. Heat Transfer 133 (8), 081504. doi:10.1115/1.4003759, Pachghare, P. R., and Mahalle, A. M. (2014). Heat Mass Transfer 55 (2122), 57225728. Therm. (2007) proposed two special structures of PHPs.